일 | 월 | 화 | 수 | 목 | 금 | 토 |
---|---|---|---|---|---|---|
1 | 2 | 3 | 4 | 5 | ||
6 | 7 | 8 | 9 | 10 | 11 | 12 |
13 | 14 | 15 | 16 | 17 | 18 | 19 |
20 | 21 | 22 | 23 | 24 | 25 | 26 |
27 | 28 | 29 | 30 |
- MelsecNet-G
- pc제어
- REGULATOR
- RS232
- CDG
- 레귤레이터
- Dry etcher
- melsec
- pressure
- Polling
- ION Gauge
- rs-232
- VACUUM
- Gas box
- 가스
- Helium
- 자동제어
- MODBUS
- gauge
- 설비제어
- c# build date
- 시리얼통신
- 폴링
- rs-485
- DATAGRIDVIEW
- HI-Vacuum
- PMAC
- 드라이에쳐
- hivac
- cluster
- Today
- Total
진공에 대해 알려주마.
PLC 그리고 PC 본문
by BOT
반도체 혹은 디스플레이 업계에서 장비 제조를 시작하여 어느 정도 규모로 성장하게 되면 가장 걸림돌이 되는 부분이 제어 부분이다.
많은 회사들이 장비 개발을 위하여 설계, 전장, 제어 그리고 공정으로 업무를 분장하게 된다. 가장 큰 역할을 하는 것은 역시 설계업무이다. 하드웨어가 구성이 되어야 그 나머지도 존재하게 되기 때문이다.
하드웨어 설계는 초기에 가장 많은 업무 로드(load)가 발생하지만 고객사 납품 후 설비가 안정화될수록 업무가 줄어들기 마련이다. 전장 업무는 있는지 없는지 중요한 것 같으면서도 아닌 것 같기도 하고 가장 비중이 낮은 업무일 수 있으나 없어서는 안 될 부분이기도 하다.
제어는 설비 설계 초기 부터 무언가 바쁘게 하는데 성과는 없고 장비 따라 나가더니 복귀할 생각은 안 하고 도대체 뭐 하는 거야. 어디에서나 주변 부서이고 일하는 것 같지도 않고 제어 사고는 자주 발생하고 해결은 잘 안 되고 구라 치는 것 같고 어렵다고만 하고 이넘들을...
어떤 장비 회사에서는 아주 훌륭한 GUI(화면)을 가지고 있었으며 제어도 아주 훌륭하게 동작하고 있었으나 얼마 이후 출하된 장비에서는 그 보다 못한 화면과 버그 많은 구동 상태를 보았다. 그 회사에 대해 들은 이야기와 장비 상태를 관련지어 추정해 보면 제어를 맡은 인원이 누군가에 따라 전혀 다른 회사의 장비처럼 나타나게 된다.
앞의 설비는 뽀샵과 디자인 그리고 장비 운용에 일가견이 있는 고수이고 뒤의 설비는 인수인계받은 신입이나 아니면 외주 개발일 것이다. 물론 화면이 화려하다고 좋은 설비는 아니지만 같은 성능에 화면빨이 좋으면 좀 더 낮지 않겠는가?
간단한 장비의 경우 PLC와 터치 모니터를 이용하여 구성하면 가장 효율적이고 안정적으로 장비를 운용할 수 있다. PLC가 융통성이 없어 지정된 동작만 완벽하게 처리하기 때문에 이 보다 더 좋은 제어 장치는 없을 것이다.
하지만 규모가 커지고 정밀해지며 다양한 운영 방법을 요청받았을 때는 PLC 이상의 제어가 필요하게 된다. 그 외에도 대용량의 데이터 처리와 많은 정보를 표시하고자 할 때 그리고 무엇보다 고객의 요청이 있는 경우 PC를 고려하게 된다.
PC 제어를 위하여 외주를 써야 하나 아니면 PC 제어 인원을 한 면 뽑아야 하나 고민이 시작된다.
외주의 경우 웬만한 요청사항은 잘 들어주는 편이다. 외주사가 가지고 있는 역량 내에서는 기대 이상의 효과를 볼 수 있다. 장비가 납품되어 운용되다 워런티가 만료된 이후에 발생되는 기능 개선, 설계변경, 고객 요청 등을 처리하려면 또 다른 고통의 시작이다. 물론 비용만 빵빵 히 준다면 아무 문제가 되지 않으나 원가 절감은 설비 업체의 최대 목표이므로 예상한 결과가 나타나게 된다.
그럼 PC 제어 인원을 뽑아서 다 시켜보자.
신입은 뭘 해야 돼지를 고민하고 중급자는 바로 짐을 쌀 것이고 고수는 의리나 자존심으로 결국 해낼 것이다. 그리고는 인수인계받은 신입사원이 모든 걸 원래대로 되돌릴 것이다.
이런 고민 해결을 위하여 몇 가지 정보를 기술하며 이것이 선택에 도움이 되었으면 한다.
1. PLC제어
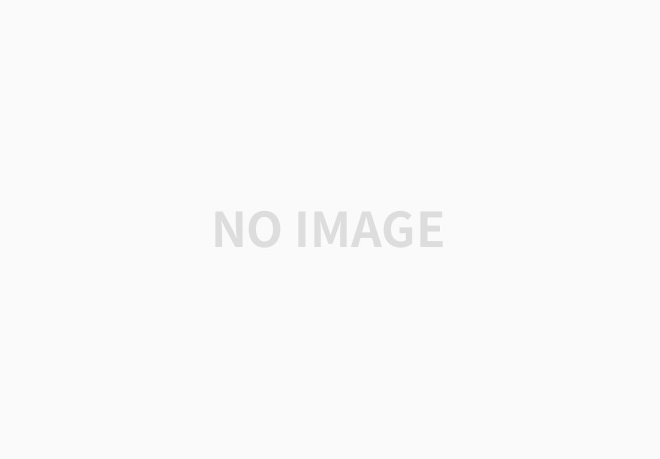
PLC 본체와 디스플레이(GOT)를 연결하여 사용된다. 설비를 PLC로만 제어하는 경우는 많은 장점이 있다. PC 제어와 비교하여 상대적인 평가이다. 물론 PLC Laddar로 어떠한 설비든 제어가 가능하나 클러스터 타입의 설비 보다 한 개의 챔버 혹은 한개의 독립 설비를 제어하는데 유리한다.
- 모션 구동이 많은 설비
- 장시간 공정이 필요한 설비 (PC Down 등의 문제가 없는)
- 열을 이용한 설비처럼 끊기면 문제가 많아지는 설비
- 초고속 운전 설비
- 매우 반복적인 공정을 진행하는 설비
PLC는 거의 중단 없는 운전을 계속할 수 있다. PC처럼 업데이트를 위하여 설비를 멈추지도 않고 빠르며 거의 down 되지도 않는다. 그러면서도 겁나 빠르다. 싱글 스레드를 사용하는 프로그래밍 언어와 같은 방식으로 사용된다.
함수를 동시에 운영할 수 없고 무조건 순차적인 수행만 가능하다. (PC에서의 BASIC 언어처럼 말이다.)
더 강점은 국내에 PLC 엔지니어 층이 굉장히 많다는 것이다. 업계는 미쓰비시 PLC가 주로 사용되어 개발, 유지 보수를 위하여 필요한 엔지니어 층이 굉장히 두꺼운 편이다.
PLC 프로그램과 주소용 엑셀만 잘 관리하면 누구를 데려와도 유지보수가 가능하다.
2. PLC제어 + PC GUI, DATA 관리
PLC를 사용하다 보면 가장 아쉬운 부분이 있다. 데이터 관리와 화면이다. 설비를 운영 중에 발생하는 history를 보관 관리 하여야 하는데 PLC로는 그 한계가 있다. 설비가 운영 중 발생하는 경고와 알람 그리고 데이터 로그 등을 관리하려면 PC가 필요하게 된다.
어차피 데이터 관리를 위하여 PC를 사용하게 됐으니 화려한 GUI로 같이 사용해 보자는 구조이다. PLC에서 모든 데이터를 access 하여 시간별, LOT별 구분 저장, 호출하여 화면에 보여주는 것이 기본이고 현재 설비 상태를 화려한 화면빨로 표시하자는 것이다. 확실히 PLC화면보다는 PC가 화려하다.
PLC와 PC의 장점만 가져와 시너지 효과는 발생한다. 단점으로는 서비스를 위하여 두 명의 엔지니어가 출동해야 한다는 것이다. 한 명의 엔지니어가 작업이 가능하면 최상의 조건이 된다.
이전에도 열장비에 반송 시스템 그리고 FA(CIM)을 사용하는 설비를 개발하였는데 상당 기간 동안 PLC+PC+CIM 엔지니어가 라인에 상주했어야 했다. 어느 시점부터는 모두를 혼자 해야...
3. PC 제어
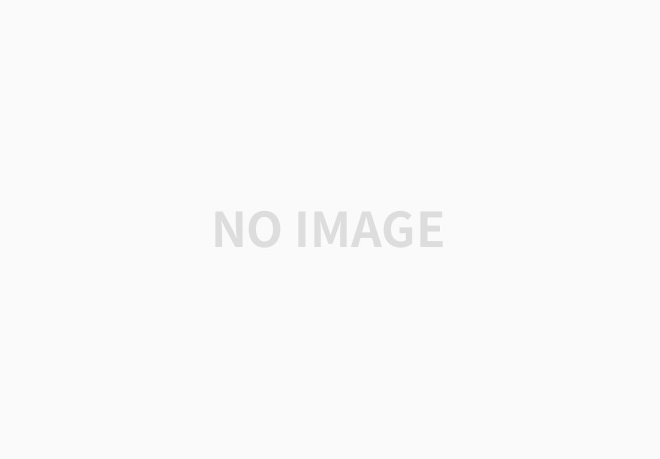
반도체 업계는 많은 설비를 PC로 제어한다. 반도체 설비 산업 초기에는 당연히 PC로 제어하였으며 많은 융통성을 부여하였다.
반도체에서 디스플레이로 넘어오면서 PLC가 업계에 많이 사용되었다. 고객의 요청도 있었지만 PLC의 발전과 손쉬워진 사용법이 시장을 넓혀간 것이다.
PLC는 개발 툴(설비를 제어하기 위하여 사용되는 개발환경)이 한 개다. 모든 엔지니어가 동일한 툴을 사용하여 설비 제어 프로그램을 만들게 된다. 개발 1~2개만 하면 그것을 응용하거나 얻어온 프로그램으로 계속 확장해 기능을 개선하고 버그를 줄여 나갈 수 있다.
하지만 PC는 사용하는 환경(Windows) 이 매번 바뀌고 개발환경(Visual studio, C++, C#, Basic 등)이 서로 다르고 하여간 많이 다르다. 이를 손쉽게 해결하는 방법은 Frame work이라고 해서 PLC의 개발 환경처럼 설비 개발을 쉽게 하기 위하여 개발 환경을 구성해 놓는 것이다.
Frame work을 구성해 놓으면 사용하고자 하는 장치 혹은 I/O Module의 통신 프로그램만 구성하면 장치의 접근이 가능해진다. 작업량을 현저히 줄일 수 있는 장점이 있다.
많이 PC 엔지니어가 각기 다른 frame work을 가지고 다니며 설비 제어 프로그램에 적용하곤 한다. 간혹 훌륭한 frame work이 만나기도 한다. 또한 이미 업계에서 검증된 frame work도 있으며 이는 검증된 만큼 비싼 사용료를 부담해야 한다. 이러한 이유로 PC는 관리가 쉽지 않으며 많은 경험이 있는 관리자가 꼭 필요한 이유이다.
Frame work에는 다음과 같은 내용이 구성되어야 한다.
메인화면
설비 전체의 상태를 확인할 수 있어야 한다. 설비마다 모두 다르기 때문에 설비에 맞추어 만들어져야 한다. 단독 설비의 경우는 설비의 진행 상태 등을 표시하고 클러스터 타입은 개별 챔버의 상태를 모두 표시하여야 한다.
레시피 화면
독립 설비는 설비를 운영하는 레시피만 필요한지만 클러스터, 배치 설비의 경우는 거기에 필요한 항목이 추가되어야 한다. 당연히 레시피를 편집할 수 있는 화면이 필요한다. 이는 시스템의 구성마다 다르므로 준비하고 사용치 않는 것이 효율적이다.
메인트(수동동작) 화면
자동 운전이 아니고 부분동작, 설비수리, 테스트가 필요한 경우 사용되는 화면이다.
히스토리
알람 히스토리, 설비동작 이벤트, TACT 관련 이벤트, 장치 간 통신 내역,
히스토리에서 중요한 것은 이벤트 레벨을 지정할 수 있어야 한다. TACT를 확인하기 위해서는 Sequence 레벨에서 확인이 가능하여야 하고 장치의 통신 문제를 드라이버 통신 레벨에서 확인하여야 한다. 다시 말해 이벤트의 발생이 내려 갈수록 저장되는 파일의 커지므로 저장 레벨이 조정 가능해야 하며 저장시간을 확인하여 자동 삭제가 가능해야 한다.
알람 화면
현재 발생한 알람의 내용을 확인할 수 있어야 한다. 주로 팝업창으로 구성하며 현재 발생된 알람의 ID, 내용, 알람의 경/중(Warning/Alarm) 상세 내용 등을 표시할 수 있어야 한다. 여기서 클리어된 알람은 히스토리에 남아야 한다.
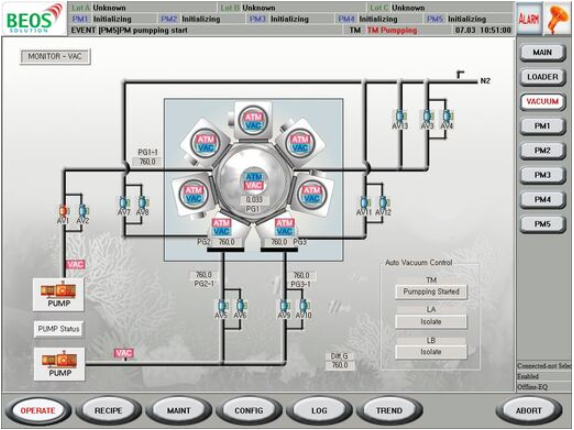
추후 관련 자료를 추가하겠다.
'진공 > 장비' 카테고리의 다른 글
AOI(자동광학검사) (3) | 2021.11.25 |
---|---|
REGULATOR (레귤레이터) (0) | 2021.08.09 |
ETCH PROCESS (4) | 2019.11.17 |